Requiem for the splicer or anatomy of the failure.
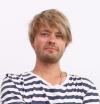
Despite the silence on the site and very serious stress in my life, there was some movement here, I made several units that where distributed in Switzerland -to friends, FabLab Zurich and Hochschule Luzern among the others- but I failed when I attempted to mass-produce copper pieces in-house. But let's analyze errors and lessons learned step by step:
MARKETING
How do you achieve that? At that time (2014) I could not launch Kickstarter campaign since back then Swiss companies where not able to do so, Indiegogo on another hand sounded a bit too shallow and small. Plus there was a PayPal requirement and as someone who had experience with PayPal as a seller I truly *hate* the bastards with a passion and try to avoid giving them any business as much as I can. So I decided “hey, I have my own payment gateway, my servers to run sites on, let’s try my own pre-order system”.
Lesson 1
Bloody obvious marketing, marketing, marketing…. Spread the word, contact all news sites and blogs you can find, tell them you have something interesting. Most of them actually look for things to post and they would take your idea and make entry with it.
Lesson 2
If you can: Go with large crowd funding site… apply lesson 1 on top.
SUPPLY CHAIN
Even if I would have followed the both lessons and succeeded in marketing, I think that my project would fail (or cause me great grief). Reason? I did not have proper supply chain in place…
You see, when you make a prototype things look very simple, you order some parts from AliExpress or some other Chinese site, you measure them, make your prototypes to fit together and think that this is the way it will work when you will produce things en-masse. *Good luck* to you. What will really happen is that next time you will order Ceramic Heaters, PID Controllers etc. -even from the same seller- you will get things that are slightly different:
- You will get Ceramic Heaters that are not 4.9mm in diameter but +/- .1mm, so they do not fit into or too lose in the the holes you drilled in copper parts.
- You will get deformed probes on PID controllers.
- Those shiny 12V power plugs for the back of your device will have shaft of 8mm but thread will end at 6mm instead of 8mm as it was in previous batch, so you will not be able to fix them in 6mm plywood.
- And… and… and…
Chinese suppliers (As well as some western ones) often lack consistency in their batches. I knew that back from the day when we run textile business but I thought it would be a bit better with electronics / hardware components. Fool…. Risk of bad consistency is a bit less within a single order but even there it can strike you.
Lesson 3
Find consistent and reliable partners for all components BEFORE you launch your Crowd Funding campaign. Yes, reliable partner will cost you (quite a bit) more but trust me, it is worth it! If component is cheap enough you can also take the risk and buy large ‘AliExpress’ batch in advance, but you risk ending up with lots of useless things if campaign fails.
IN HOUSE PRODUCTION
Oh boy…
When I initially made splicer, only facilities I had in house was a Laser Cutter and wood / aluminum router. I always wanted to have a real metalworking workshop so it came that in recent 2 years I have heavily upgraded, to real albeit light milling machine (EMCO FB3), lathe (Sieg SC10), grinder, saws, stock, tooling, measurement, sanding equipment etc. It is amazing how much money you can sink into that and even then, you miss proper tools all the time. I put about 15k $ into it all.
Luckily only some parts I had to order specifically for splicer (1.75mm convex cutter that set me back almost 300$).
As a total novice in metalworking I read books, watched with fascination videos of Abom79, MrPete222, Keith Rucker and Metal Tips and Tricks, trying to learn. I went through stock material and tooling like through butter (Peng, there goes your 35$ spiral tap), but I learned.
I produced several splicer copper components in house and it worked wonderfully, the final result was much better then prototype, I was very proud to hold those quite complex pieces in my hands and see how well they fit together. But there was one problem: It took me almost 3 hours for each splicer, so I had to optimize, not cut one piece at a time but do 5-6 of them, so I can spare myself entire re-alignment and tool changes.
THIS is where real problems start, you begin to realize how complex it is to align 6 copper blocks in perfect line, you make mistakes by mis-aligning work pieces or tooling and one mistake ruins not one but 6 pieces. You realize that your used milling machine has a problem in that Z-axis shifts by up to .1mm as you move table on X axis. You realize that your Chinese vice does not hold multiple pieces properly. And and and. But I went through it all, fought, learned and at last when I was left with enough stock material for 17 units I thought that I am ready. xoxoxo
I wanted this to be perfect, so before I started the “production” I brought my 3mm convex cutter to grinder company to ensure it will be razor sharp! I am sure experienced metal workers will see where I am going to here….. You see, when you re-grind your tools their diameter often changes… so when I got my cutter back it was not 3.00 but 2.75mm. And I forgot about it, it read R1.5 and I assumed it is R1.5. Fool!
My next mistake was not to control the cuts after each run. This was fatal, so after almost 10 hours of labor I ended up with total of 34 70% done blocks (main heating and cooling blocks), nicely cut but entirely useless since the slots where too bloody small for 3mm filament! And no, you cannot just re-fix blocks in vice and run larger cutter because it is impossible to get proper alignment again, especially with several blocks together. This was when I finally said F.CK IT and went to sleep. Next morning I thought to repeat attempt but then I remembered that I simply had no more stock material left. That sealed the faith of Splicer.
Lesson 4
Always control and measure after every step of your work, double check your DRO before cutting, do visual control etc. Make control after each step essential part of your ‘routine’.
Lesson 5
Let *professionals* do mass production for you, especially with such unforgiving thing as metalworking. Having your own workshop is nice but keep it for prototyping only, DO NOT attempt to mass produce, save your soul! By the way, I am interested to hear how this (small in-house production) applies to electronics, is populating and re-flowing PCBs in house as hard and fail-prone as metal working?
EPILOGUE
While I failed to sale or produce meaningful numbers of the splicer, one should not forget that it was never intended to be a real, serious product, it was a pilot project to try out the waters and learn from it. As such it has fulfilled it’s role perfectly, I have learned a lot during this time and it will surely help me in future.
Thank you to everyone who liked the idea, I really appreciate your trust and encouragements and if life permits, hope to come back to Maker community with new, exciting and properly setup projects in close future!
6606 Comments
Hi Kirill, thanks for full
otto (not verified)
onWed, 03/09/2016 - 00:27
Permalink
Hi Kirill, thanks for full and colourful description of your labour. I commiserate with you whole-hartily. I know exactly where are you coming from. I am retired, I hoped for a quiet retirement, as I had a factory in the past making microfilm equipment. But came 1980 CD ROM and it killed me (almost). 4 years ago I got bitten by the 3D printing bug, designed printer, and set about making it. Previously I had a factory, lot of space, tool room, plastic processing, injection moulding, vacuum forming, you name it I was making things in house. It all went. When I started getting quotes from professionals for parts, they were either too expensive, or unrealistic quantities. So I ventured about equipping myself from scratch. Bought CNC lathe and mill, developed technigue to repeatedly clamp small parts, as heater blocks etc, precision cutting of rods and extrusions. Now fast forward, there is a new printer announcement almost every day, so one has to have something special to get some attention. What I learned so far, is to design the precision out of the product, not meaning to make rubbish, but to achieve precision by a clever design, utilising as many standard parts as possible. Also my problem is being distracted easily, not focussing on the target and getting off on the tangent. So I wish you a good luck, use cheaper materials, if you can, e.g. aluminium instead of copper is good enough, cheaper and easier to machine. All the best, otto
C
rcraawwlleerrgg... (not verified)
onMon, 03/28/2022 - 22:12
Permalink
C
C
rcraawwlleerrgg... (not verified)
onMon, 03/28/2022 - 22:12
Permalink
C
C
rcraawwlleerrgg... (not verified)
onMon, 03/28/2022 - 22:12
Permalink
C
C
rcraawwlleerrgg... (not verified)
onMon, 03/28/2022 - 22:12
Permalink
C
Cr
acwrlaewrlegrog... (not verified)
onFri, 04/01/2022 - 04:00
Permalink
Cr
Cr
acwrlaewrlegrog... (not verified)
onFri, 04/01/2022 - 04:00
Permalink
Cr
tmpjnrqcsogssxebplxv
rcraawwlleerrgg... (not verified)
onMon, 03/28/2022 - 22:58
Permalink
tmpjnrqcsogssxebplxv
C
rcraawwlleerrgg... (not verified)
onMon, 03/28/2022 - 22:58
Permalink
C
C
${@var_dump(md5... (not verified)
onMon, 03/28/2022 - 22:58
Permalink
C
C
rcraawwlleerrgg... (not verified)
onMon, 03/28/2022 - 22:58
Permalink
C
C
rcraawwlleerrgg... (not verified)
onMon, 03/28/2022 - 22:58
Permalink
C
ronrrlvsfxlcnemgoiau
rcraawwlleerrgg... (not verified)
onMon, 03/28/2022 - 22:58
Permalink
C
${958050749+861780427}
rcraawwlleerrgg... (not verified)
onMon, 03/28/2022 - 22:58
Permalink
${958050749+861780427}
C
rcraawwlleerrgg... (not verified)
onMon, 03/28/2022 - 22:58
Permalink
C
C
'-var_dump(md5(... (not verified)
onMon, 03/28/2022 - 22:58
Permalink
C
C
rcraawwlleerrgg... (not verified)
onMon, 03/28/2022 - 22:58
Permalink
C
C
rcraawwlleerrgg... (not verified)
onMon, 03/28/2022 - 22:58
Permalink
C
C
rcraawwlleerrgg... (not verified)
onMon, 03/28/2022 - 22:58
Permalink
C
I commiserate. You were
PhilM (not verified)
onThu, 04/28/2016 - 23:22
Permalink
I commiserate. You were wondering about PCB DIY production. Same experience making electronics. I had some great brain-storms and was sure people would use my idea. I think all small-scale startups fase the same chicken-vs-egg connundrum: Too expensive to achieve economy of scale through high volume production, impossible to meet consumer expectations for dirt-cheap gadgets. Much of this is due to the Chinese manufacturing economy. I don't blame them for growing their economy even if they don't play by western rules or ethics, but that does not change the fact that they have made the traditional garage-shop startup a practical impossibility for most industries, at least in the U.S., and probably for most industrial nations. I blame our political class for selling us all out in exchange for cheap/easy treasury loans. Maybe you can find some niche they haven't exploited yet. Just don't expect to make a carreer of it. --PhilM
Hi Artesea, great article! I
Michael G (not verified)
onThu, 07/21/2016 - 06:09
Permalink
Hi Artesea, great article! I've attempted to pick up the baton of manufacturing a filament fusing tool, and I was able to deal with many of the issues you've discussed here by manufacturing them myself in small controlled batches. The control issue was dealt with by plugging the device into your 3d printer controller. More info here: http://3dprinting.com/how-to/fuse-filament-home/
Yes it is hard to get an good
Preben Frederiksen (not verified)
onFri, 10/14/2016 - 03:47
Permalink
Yes it is hard to get an good idea go true.
If you have parts enough back, to make one more filament splicer, I could be interested.
Preben Frederiksen
Denmark
pcdoctor@mail.tele.dk
Thank you for the sage advise
Kent Hartland (not verified)
onTue, 03/28/2017 - 16:46
Permalink
Thank you for the sage advise. Legions of us are following in your troubled footsteps with hope and confidence that we shall pick up the banner and march forth to victory. Ye verily.
So, I'd like to know what you've decided to do next now that you've had a bit of a sabbatical. You can't go out there and look at all that nice equipment without great pangs of guilt and shame. ?There must be some idea niggling you, demanding that you get back to work. Failure is not your name.
Kent@DamnSolidDesign.com
Next Time: www.TechShop.com
Pete Aronson (not verified)
onTue, 04/25/2017 - 00:53
Permalink
Next Time: www.TechShop.com
Most of my products I produce right there in "My" 15,000 sq/ft Machine Shop.
www.ExpensiveLightweightStuff.com
Great insights and sorry that
Tom (not verified)
onMon, 06/12/2017 - 22:59
Permalink
Great insights and sorry that it ultimately did not work out for your - but lessons learned are invaluable and your next project will be a success (and it only needs one success...).
Thanks again for sharing!
Tom
i really really really would
mitchell hirsch (not verified)
onTue, 06/13/2017 - 22:28
Permalink
i really really really would like the copper part, or the details of making one!! are you able to make this happen???? email me @ mitchhirsch@icloud.com
I would like to buy one, put
Nic (not verified)
onSat, 02/24/2018 - 02:25
Permalink
I would like to buy one, put it on Etsy.
RE:Order not good
Randi Onus (not verified)
onTue, 06/23/2020 - 22:47
Permalink
Hello
My package was damaged for the second time.
I made a picture so that you can see what I mean. https://imgurgallery.com/df5thj7
I hope you can help me solve this problem.
Regards
Randi Onus
"Sent from my Samsung"
RE:Order not good received.
Dolores Neild (not verified)
onTue, 07/14/2020 - 11:37
Permalink
Hi
My package was damaged for the second time.
I made a picture so that you can see what I mean. https://imgurgallery.com/hu76tfr
I hope you can help me solve this problem.
Yours truly
Dolores Neild
"Sent from my Samsung phone"
Cristopher
Bernie (not verified)
onTue, 04/13/2021 - 21:41
Permalink
Want to find more serious customers for your online business? We can deliver niche targeted traffic tailored for your business model For more info Visit: http://bit.ly/hi-quality-web-traffic
The technology is needed.
David Christian Dow (not verified)
onThu, 04/22/2021 - 14:48
Permalink
The technology is needed. Perhaps, with proper financial support, outside input and good old-fashioned ambition, we'll see a model soon that comes to market at an acceptable cost of investment. The splicer paves the way for many types of filament joiners. Users have unique imaginations that require unlimited access to every conceptual tool in order to bring their visions to life. Thank you for putting in the effort to design this proof of concept model so that people will be inspired to improve upon your vision.
Tracy Regan
Latoyia Stinde (not verified)
onMon, 07/12/2021 - 01:47
Permalink
Here is a list of 18 free traffic sources that you should be using: http://bit.ly/18freetrafficsources
Arlen Colasurdo
Loretta Haitz (not verified)
onFri, 07/16/2021 - 08:25
Permalink
Pros don't pay for ads. Here's 18 free traffic sources you should be using: https://bit.ly/18-free-traffic-sources
Doloris Bultman
Albina Worm (not verified)
onMon, 07/26/2021 - 00:11
Permalink
18 free traffic sources you should be using: https://bit.ly/18-free-traffic-sources
Clemente Winkelpleck
Moises Dieguez (not verified)
onWed, 08/04/2021 - 16:37
Permalink
Best Free Traffic Sources : https://bit.ly/resource-of-free-stuff
Marx Mcguirt
Valentin Kuerbitz (not verified)
onSat, 08/14/2021 - 15:41
Permalink
Effective And Free Ways To Advertise. Here Is A List... : https://bit.ly/free-stuff-blog
Clora Ambrosone
Meg Cordle (not verified)
onThu, 08/19/2021 - 18:42
Permalink
Unique And Creative Ways To Advertise For Free : https://bit.ly/free-stuff-resources
Dusty Leesmann
Kenton Wenske (not verified)
onThu, 09/09/2021 - 23:18
Permalink
7 Ways To Promote Your Business Online For Free https://shortest.link/OY0
Venus Gitt
Mitchel Satchell (not verified)
onMon, 09/13/2021 - 23:47
Permalink
Effective And Free Ways To Advertise. Here Is A List... https://shortest.link/OY0
Patsy Guidry
Bradford Caudillo (not verified)
onWed, 09/22/2021 - 16:19
Permalink
Best Free Traffic Sources https://t9y.me/crCX
Glenn Livermore
Elizabet Scali (not verified)
onMon, 09/27/2021 - 21:02
Permalink
Here's How You Can Advertise Your Website For Free https://t9y.me/crCX
Toby Segreto
Melodie Davidoff (not verified)
onTue, 10/05/2021 - 14:56
Permalink
Effective And Free Ways To Advertise. Here Is A List... http://www.congreso-hidalgo.gob.mx/urls/7Dw
Gilbert Cavender
Leena Bonar (not verified)
onTue, 01/11/2022 - 08:28
Permalink
Submit your site to over 1000 advertising websites for free now https://1mdr.short.gy/submityourwebsite
Mattie Ocheltree
Sheridan Kawashima (not verified)
onWed, 01/26/2022 - 03:06
Permalink
Free submission of your new website to over 1000 business directories here https://1mdr.short.gy/submityourwebsite
C
rcarwalwelregro... (not verified)
onMon, 03/28/2022 - 22:09
Permalink
C
C
rcarwalwelregro... (not verified)
onMon, 03/28/2022 - 22:09
Permalink
C
Ccrraawwlleerrggoo@gmail.com
crawlergo@gmail.com (not verified)
onMon, 03/28/2022 - 22:12
Permalink
Ccrraawwlleerrggoo@gmail.com
Ccrraawwlleerrggoo@gmail.com
crawlergo@gmail.com (not verified)
onMon, 03/28/2022 - 22:12
Permalink
Ccrraawwlleerrggoo@gmail.com
This is SUCH a great account
SirBigSpud (not verified)
onTue, 03/29/2022 - 15:52
Permalink
This is SUCH a great account of turning a hobby into a business. It can be done successfully, but to do things commercially, all the things you listed come to play. Repeatability, reliability of vendors is HUGE. I did a ton of this work while working with Xerox-spawned startups. Flying around and qualifying vendors was a big part of what I did. When each component came in different quantity deliveries, you have to factor into the price to the customer all the remnant materials/parts. Great share.
C
crraawwlleerrgg... (not verified)
onFri, 04/01/2022 - 03:58
Permalink
C
Pages
Add your comment